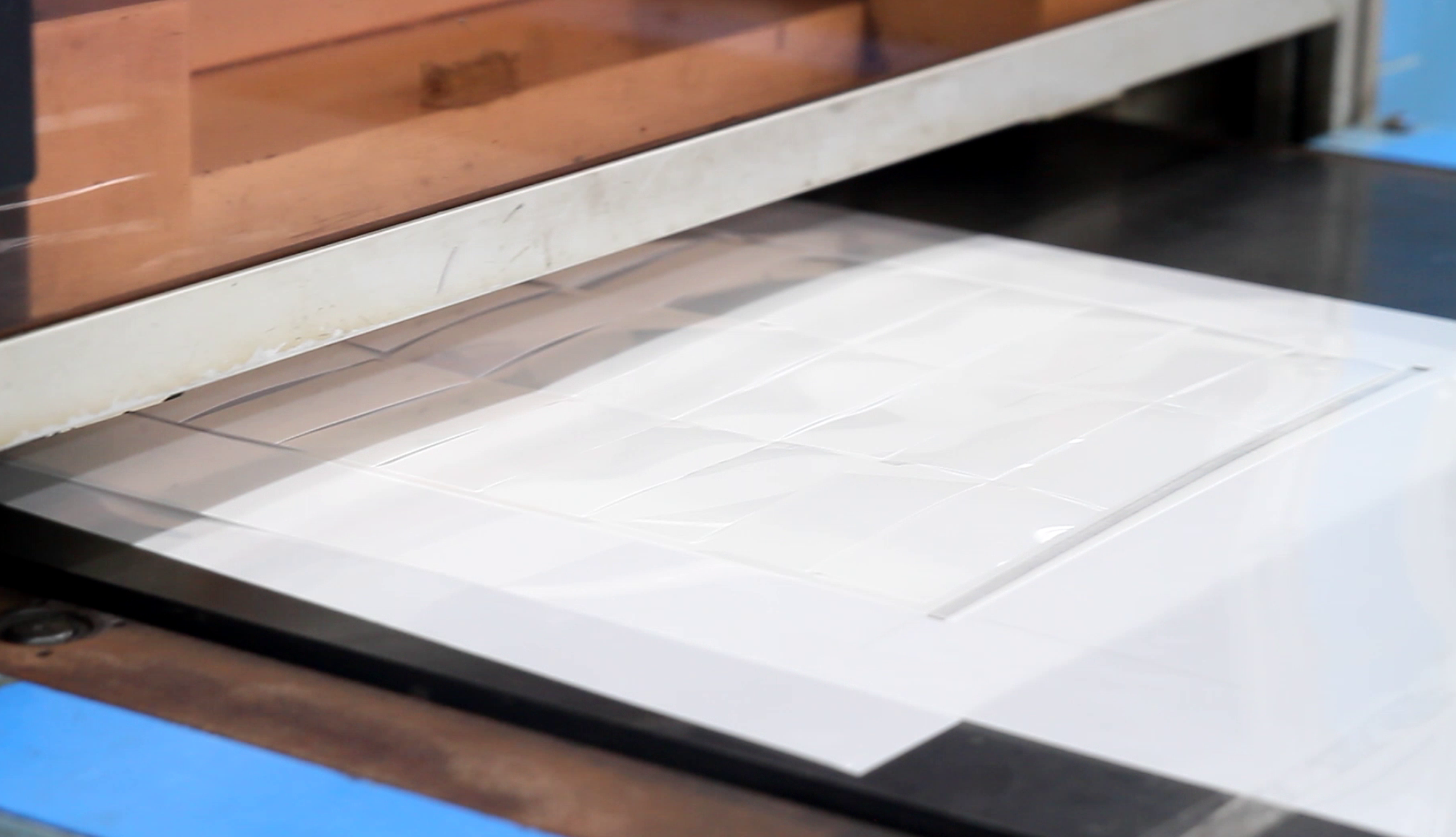
Die Cutting
We employ die cutting as a key method within our manufacturing processes to deliver precise, custom-shaped foam products. This technique allows us to efficiently cut foam materials into specific shapes and sizes, meeting the exact requirements of our clients across various industries.
Die cutting or punching refers to the process of cutting or creating holes in foam materials.
In this process, a machine uses a die, which is a specially shaped blade, to cut the foam into specific shapes or to create holes at specific points. This is similar to how a hole punch works on paper, but on a larger and more complex scale.
The specificities of the process can vary greatly depending on the requirements of the end product. For instance, the die's shape and size, the pressure used, and the type of foam material can all be adjusted to meet the needs of the product being manufactured.
This process allows for precise, repeatable cuts and is often used in industrial applications where large quantities of a specific foam shape or form are needed. For example, it might be used to create foam inserts for product packaging, foam components for furniture or automotive interiors, and many other foam-based products.
Punching is used in foam manufacturing in several applications where precise shapes or holes are required. Some of the key applications include:
Automotive: Foam is widely used in the automotive industry, particularly in vehicle interiors. Punching can be used to create custom shapes for things like seat cushions, headrests, armrests, and other interior components.
Medical: In the medical field, foam is often used for things like braces, supports, and other therapeutic devices. Punching can be used to create the custom shapes required for these items.
Electronics: In electronics, foam is often used for insulation, vibration damping, and protective packaging. Punching can be used to create the precise shapes required for these applications.
Acoustic Insulation: Foam is often used for sound insulation in studios, offices, and other spaces. Punching can be used to create custom shapes for these applications, or to create patterns that can improve the foam's acoustic properties.