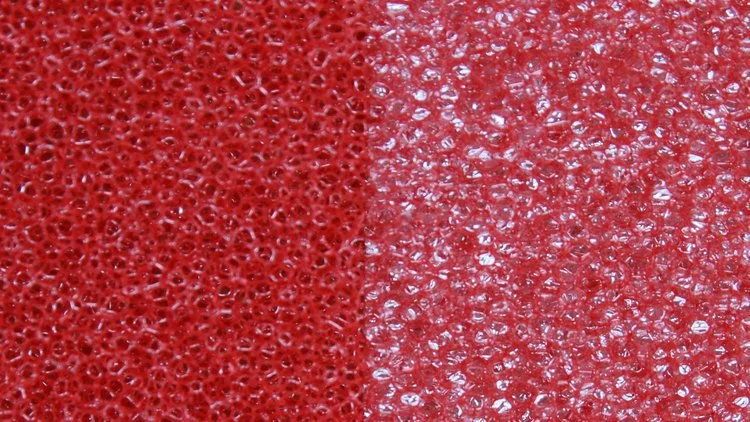
Reticulation
At Foamtec International, we utilize reticulation to enhance the functionality of our foam products. This process transforms conventional foam into an open-cell structure by removing the membranes between cells using thermal, chemical, or physical methods.
The open-cell foam resulting from reticulation offers superior porosity and permeability, making it ideal for applications requiring excellent air filtration and fluid management. These properties are crucial across various industries, including electronics, healthcare, automotive, and aerospace.
By incorporating reticulation into our production processes, we provide our customers with highly effective, customized foam solutions that meet diverse and specific industry needs. This commitment ensures our products are not only functional but also versatile and reliable.
From automobile seats and furniture to insulation and even medical applications, reticulated foam is a material that permeates many sectors of our modern life. This humble yet versatile material offers a unique combination of properties, such as high tensile strength, low weight, excellent thermal insulation, and exceptional fluid absorption, all while maintaining breathability. However, despite its omnipresence, many are unfamiliar with the science behind the process that brings it to life.
What is Reticulated Foam?
Reticulated foam is a form of polyurethane foam that has undergone a unique process to transform its structure. This skeletal framework of open cells grants reticulated foam its unique traits. While traditional foam variants have closed cells that limit fluid and air movement, the interconnected cells in reticulated foam permit liquids and gases to pass freely. This characteristic makes reticulated foam an ideal choice for applications requiring superior air or liquid flow, such as outdoor furniture, speaker grills, filtration systems, and even medical equipment.
Versatility and Applications
The unique physical properties of reticulated foam give it a broad range of applications.
In the automotive and furniture industries, reticulated foam is valued for its breathability and durability. Car seat cushions, furniture padding, and outdoor upholstery make the most of the foam's ability to permit air and water flow, preventing unpleasant odors and dampness.
In the world of audio equipment, reticulated foam is a common material used for speaker grills. Its open-cell structure allows sound waves to pass through without significant distortion while keeping dust and other particles out.
The medical field also finds numerous uses for reticulated foam. Due to its ability to absorb fluids and still maintain breathability, it's used for wound dressings and hospital mattresses. In addition, its ability to be sterilized without degradation extends its usability in various medical scenarios.
Perhaps one of the most vital applications of reticulated foam lies in filtration systems. Given its high dirt-holding capacity and the ability to allow fluid flow, it's widely used in aquarium filters, HVAC systems, and even oil filters.